Flush milling cutter for glued edges on wooden furniture parts: All-angle flush milling cutter MZ 100 160V
830,00 € without VAT.
The MZ 100 160V all-angle flush milling cutter is used to mill flush edge protrusions on the face side. Very suitable for angles deviating from 90°: Sloping roof parts, trapeze tables, bevelled fronts, bed heads, worktops. Also for flush routing top and bottom sides or corners on bevelled fronts.
We are also available to answer questions by telephone. Tel.: 05741 3012080, international: +49 5741 3012080
Description
Before: Protruding edges
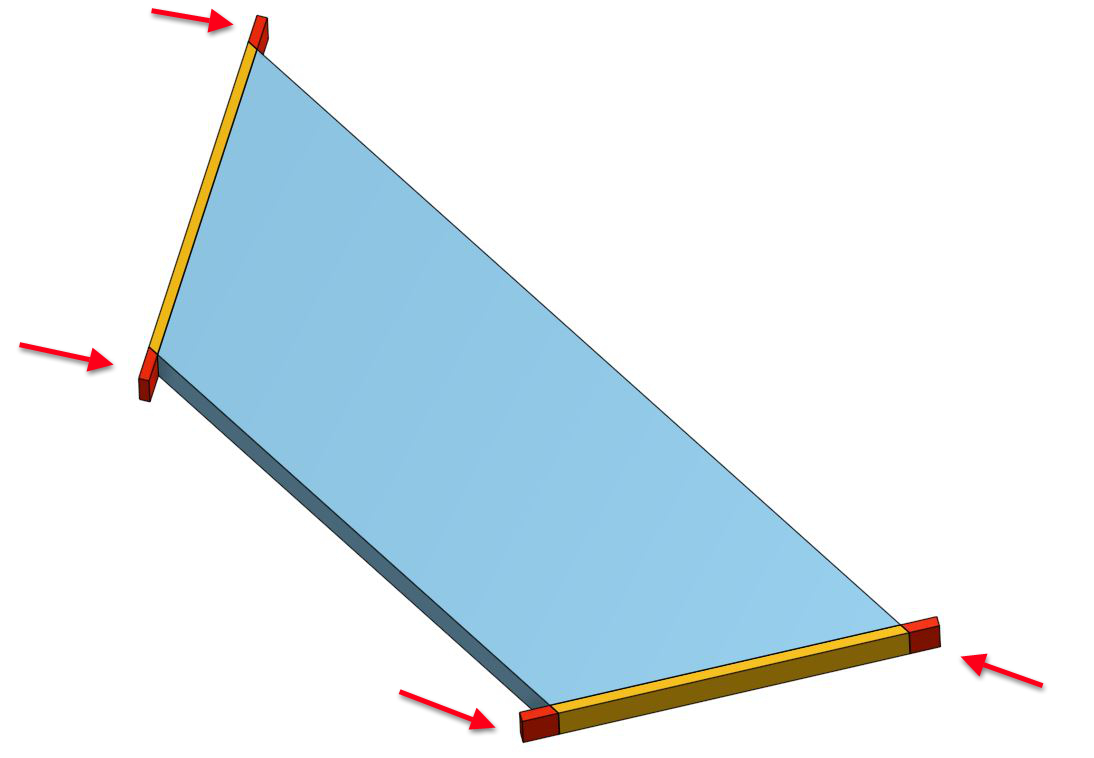
After: Flush-milled edges
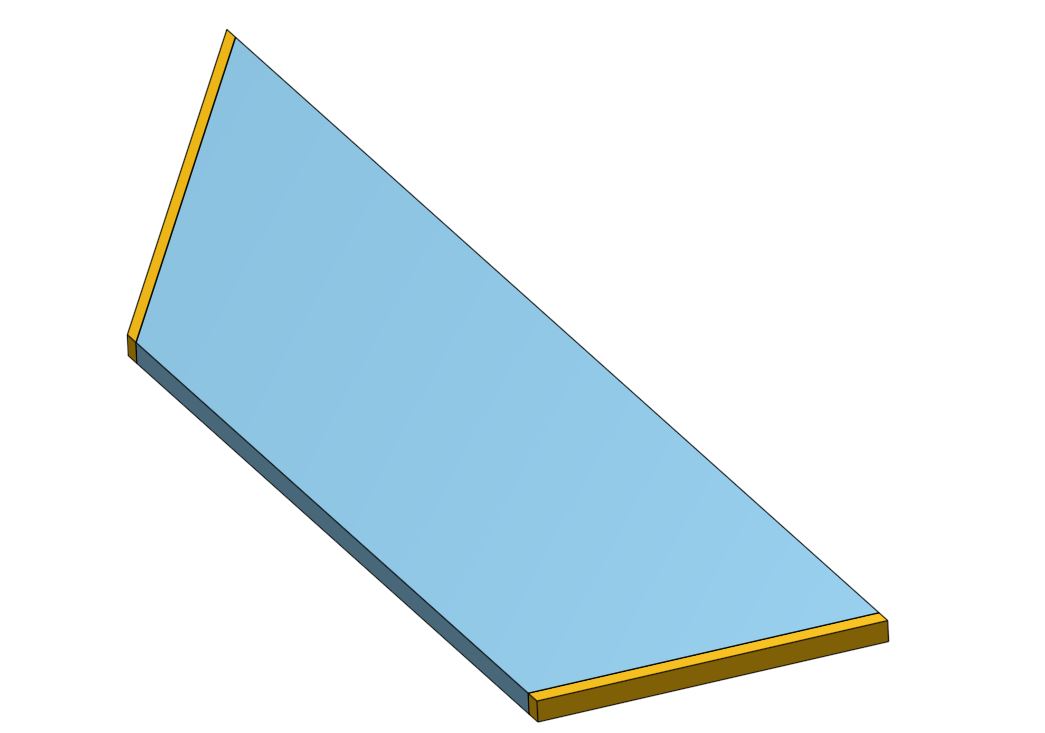
For bevelled fronts, trapezoidal tables, worktops
Our flush router is the perfect tool for glued edges on wooden furniture parts. It has been developed for carpenters and joiners. It can be used to quickly and easily mill off protruding end edges at the corners. The glued edges can be made of wood or plastic.
Unlike conventional hand-held machines, the flush milling cutter is suitable for non-angled workpieces. Examples of this are trapezoidal tables or sloping roof parts. As no stop adjustment is required, different angles can be machined directly. It is also used on right angles, for example in worktop production in the kitchen industry.
Precise milling
The flush milling cutter for glued edges on wooden furniture parts has a pneumatic drive unit. The tool is attached directly to the spindle and has a thrust bearing. The tool is a flush trimming tool. It can be used to remove the protrusions of edge strips with ease. In addition, the contact unit is rigidly connected to the drive unit. Accordingly, no moving stops need to be set. This enables simple and fast processing.
The milling cutter's thrust bearing rolls on the neighbouring edge. This keeps the cutting edges of the milling cutter at a defined, very small distance from the neighbouring edge. This enables precise machining of the protrusions. Damage to the surface of the neighbouring edge is avoided.
What the all-angle flush milling cutter can do:
- Flush milling of the edge strip overhang at corners up to α=160°
- Quick change between different angles without adjustment
- Clean milling result
- Very light, very good handling
Work quickly
- The flush milling of the edge strip overhang at corners up to approx. α=160° can be carried out easily and precisely with this milling machine.
- Thanks to the quick change between different angles, the machine can be used particularly flexibly without the need for time-consuming adjustment.
- The clean milling result speaks for the high quality of the machine and ensures a perfect surface.
- The machine is particularly light and offers very good handling, which has a positive effect on working comfort.
In short, our flush router for glued edges on wooden furniture parts is the ideal tool for joiners and carpenters who need quick, easy and precise processing of edge strips at the corners. Our flush router saves you time and increases the quality of your work. Try it out today!
Would you have thought it would go so well?
Field of application
At last a corner former for flush routing edge protrusions on angles up to 160°! And with different angles without adjustment.
Function and operation
- Air motor with carbide flush milling cutter, also with thrust bearing
- Stop rail for contact with the side of a workpiece
- Rigid yet lightweight construction made of high-quality aluminium, no casting
- Property right registered with the German Patent and Trade Mark Office
Price
With high-quality German air motor including mounted milling cutter, tested and delivered ready to mill: See above for price.
Technical requirements
The oil can be applied by means of a compressed air connection plug or, in the case of continuous operation, by means of a maintenance unit set to 1 drop of oil per minute.
Scope of delivery
- Machine
- Milling cutter, mounted and preset
- Every machine with milling cutter is tested and approved on wood/plastic
- Original equipment compressed air device oil with specification
- Operating instructions
- Tool
The all-angle flush milling cutter has been on the market since 2012 and has proven itself very well:
How it works:
1. air motor with carbide flush milling cutter, also with thrust bearing
2. stop rail for contact with the side of a workpiece
3. rigid yet lightweight construction made of high-quality aluminium, no castings
4. property right registered with the German Patent and Trade Mark Office
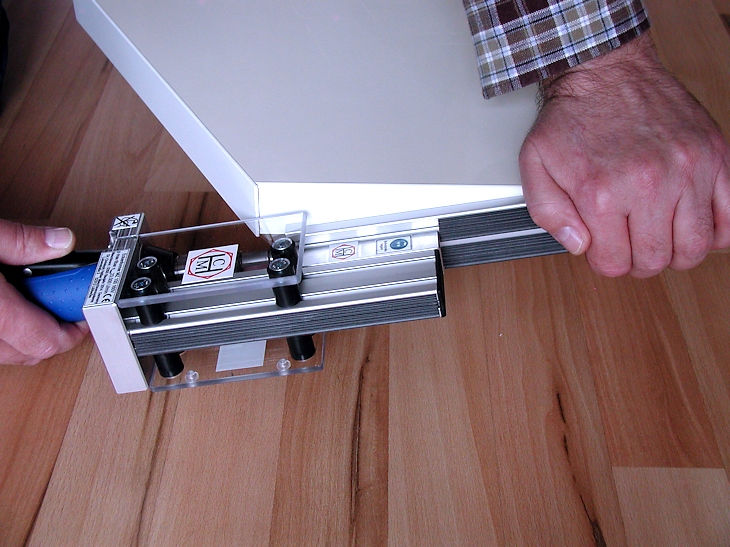
What the corner former all-angle flush milling cutter can do:
1. flush milling of the edge strip overhang at corners up to α=160°
2. quick change between different angles without adjustment
3. clean milling result
4. very light, very good handling
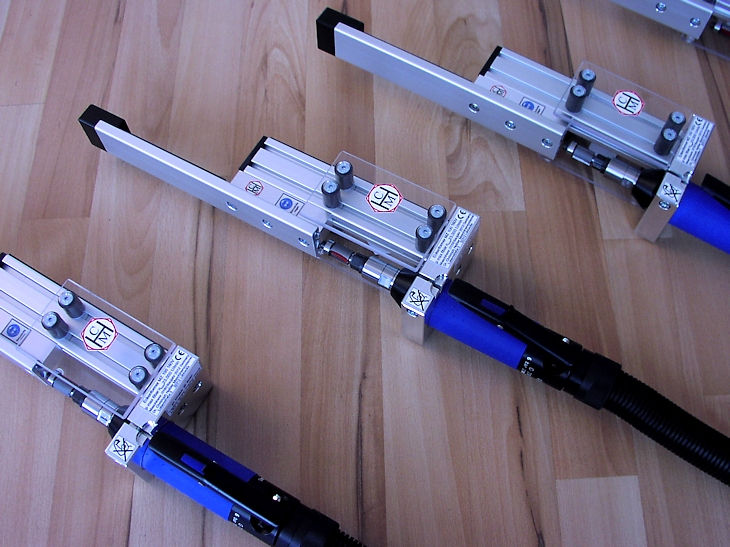
Workflow
Preparation: Roughly cut off the excess edge to approx. 3mm, max. approx. 6mm
Right corner
- Grasp the motor with your right hand at a right-hand corner.
- Grasp the stop rail with your left hand.
- Press on the workpiece with the ball of your left hand.
- The left hand forms a pivot bearing.
- The tool is swivelled from bottom to top and the excess length is removed.
Left corner:
Rotate machine around longitudinal axis, drain corresponding to right-hand corner
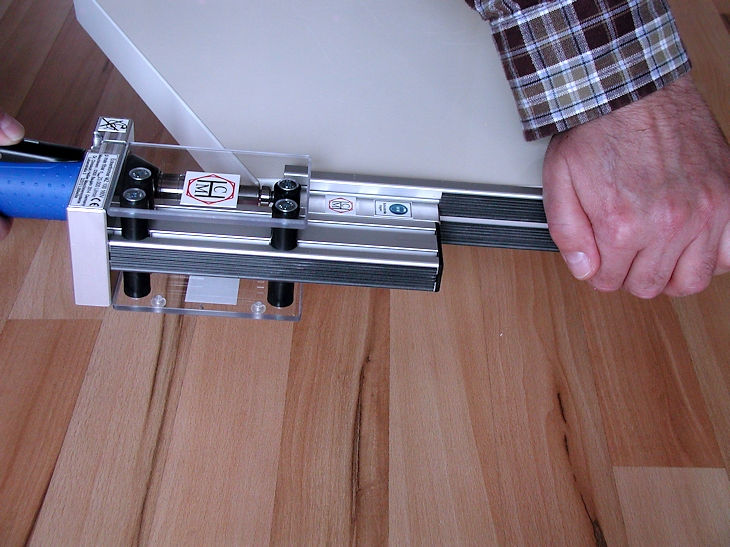
- Excellent concentricity
- Very quiet
- Very powerful
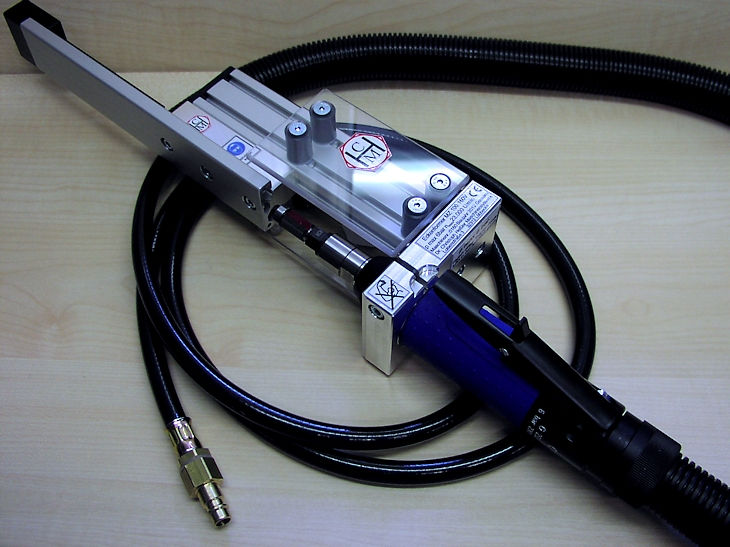
Further information
All-angle flush milling cutter
|
|
|
|
|
|
|