Corner rounding system Ecko VZ 100 90F MFK 1
320,00 € without VAT.
Corner router Ecko VZ 100 90F MFK 1 for Festool MFK 700 with through hole in the table, see pictures. Please enquire about other edge routers.
- For a perfect edge: stable, easy to handle, precise, durable
- Very easy installation, very simple and quick adjustment
- Scope of delivery: Ecko as shown, the edge router is not included in the scope of delivery.
- Alternative: Round corners with compressed air, see here
After placing an order, we will confirm the order and send you the bank details.
See video below.
Description
Task: Milling and rounding the front edge protrusion flush
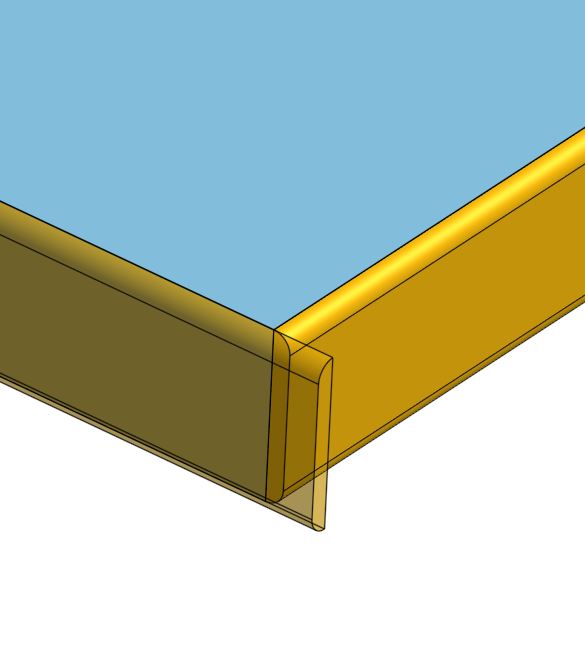
Solution: Bottom, top and side rounded corner
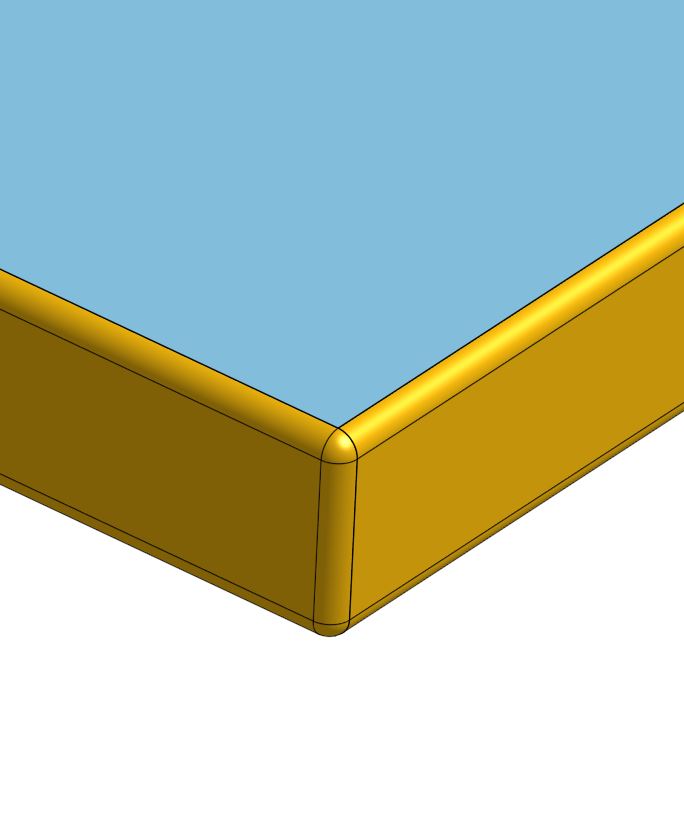
Successful corner rounding with the Ecko system
- Precisely manufactured for precise rounding
- Protection against reaching into the otherwise open milling cutter
- With adjustable stop to prevent swivelling in
Simple adjustment of the edge stop. This prevents the router from swivelling into the edge.
Field of application
Rounding of glued edges on the front side.
Compared to a copying unit on an edge banding machine, corner rounding is very cost-effective.
Function and operation
- The edge router is fixed in the corner system.
- The milling cutter's thrust bearing is guided from the first side over the corner to the opposite side.
Price
For corner rounding to be successful, precise guidance must be possible, especially with a relatively heavy, electric machine.
For example, the swivel stop is ground to close tolerances. See above for price.
Technical requirements
- The milling cutter must have a thrust bearing.
- The machine must have a through hole in the table for the M8 threaded pin of the swivel stop.
- The brown support surface of the table must end in front of the milling cutter. If the support surface encloses the milling cutter, please let us know. We will then adapt the Ecko accordingly.
Scope of delivery
- Swivelling stop
- Table with guard
- Collar insert
- Modified thrust bearing brake
- Operating instructions
Further information
The Ecko system is mounted on an edge router. In the version offered here with the designation Ecko ...MFK 1, the Festool MFK 700 edge router becomes a corner rounder.
The Ecko system consists of 3 assemblies
- Swivelling stop
- Table unit
- Collar unit
Corner rounding is a success with the Ecko. The three main sources of error in corner rounding are avoided: vertical wobbling of the machine, horizontal wobbling and warping at the end point.
Assembly is very easy to carry out. The operating instructions are richly illustrated. The stops can be adjusted quickly and easily.
The swivelling stop 2 is fastened through a through hole in the machine table. The swivelling stop 2 has a large diameter so that it can be tightened by hand without tools. Like the other white components, the swivelling stop 2 is made of high-quality engineering plastic. In addition, the swivelling stop 2 is ground with extreme precision so that mechanical engineering accuracy can be achieved despite the light weight of the plastic.
Table 1 is slid onto the swivel stop 2. Table 1 contains the swivel bearings 8, 9 with a very precise bearing bore. The swivel bearings are aligned with each other via pockets milled into the slide plate 7. The table is fixed in place without tools using a spring-loaded locking bolt 12.
On the one hand, the table 1 can be safely guided with the handle of the table 32. On the other hand, the guide hand is fixed to the location of the handle and is far and safely away from the milling tool. In addition, the tool is prevented from engaging by a chip and engagement guard 10.
The edge stops 17, 33 prevent warping at the end point. In the case of a right-hand corner, the end point of the routing path is defined by the contact of the collar clamp on the workpiece. The edge stops 17, 33 are set so that they are in contact with the workpiece at the latest at the same time as the collar clamp.
The components of the Ecko system
1 Ecko VZ 100 90F MFK 1
2 Swivelling stop
3 Table unit
4 Collar unit
5 M8 grub screw
6 Nut M8
7 Slide plate
8 Bearing bracket right
9 Bearing bracket left
10 Chip and intrusion protection
11 Handle plate
12 Locking bolt
13 Right edge stop
14 Left edge stop
15 Edge stop holder
16 Spring-loaded thrust piece
17 Right edge stop
18 Star grip
19 Collar
20 Collar clamping, in contrast to the brake 25 Shortened at the end face
32 Handle
33 Left edge stop
34 Star grip
35 Stop side
36 Stop side
The collar 19 is inserted into the opening of the table and held by the collar clamp 20. The collar 19 ensures that the cutter is turned around the front support point of the machine table in the direction of the workpiece, which would otherwise immediately destroy the edge surface.
The Ecko system takes into account two further points that affect the edgebanding process on a workpiece. After gluing on the edgeband, the longitudinal edge is first processed on the top and bottom sides. The router is set for this. When changing to corner processing, the machine with the router is turned from vertical to horizontal. On the underside and top side of the workpiece, the contour of the previous longitudinal edge milling is also painted over again by hand during corner processing. There is a very high risk of unsightly milling marks appearing here due to asymmetry in the milling cutter and operator-dependent guide inaccuracies. For this reason, collar 19 can be ordered so that it protrudes slightly in front of the sliding plate of the machine, thereby retracting the milling profile. The edge is protected and there is no need to readjust the milling cutter.
Now you have created a right-hand corner, where you guide the machine with your right hand. Now what do you do with the other corner of the workpiece side, called the left corner? Especially with large workpieces that are not easy to turn. This is very easy with the Ecko. With one hand you press the table 1 onto the workpiece via the black handle 32 and with the other hand you swivel the machine from one side to the other, held securely by the swivel stop 2.
It is always routed in the opposite direction, i.e. from bottom to top for a right-hand corner. The front edge overhang should be trimmed. The shorter the overhang, the better the milling result. The router's thrust bearing is placed against the workpiece and guided upwards from the bottom to the top. The hand on the Ecko table follows the movement.
Corner rounding is easy with the Ecko.
The Ecko system is registered as a property right.
If you have any questions, please do not hesitate to contact us: Phone: +49 (0)5741 3012080