All-angle flush milling cutter MZ 100 160V H
2.490,00 € without VAT.
The all-angle flush milling cutter H is used to mill flush edge protrusions on the face side. In contrast to the Standard flush milling cutter complex components can be machined with the H variant. Very suitable for so-called puzzle parts and other special parts. Proven in the manufacture of caravans and mobile homes. There is a right-hand version as shown and a mirror-image left-hand version.
We are also available to answer questions by telephone. Tel.: 05741 3012080, international: +49 5741 3012080
Description
The working principle
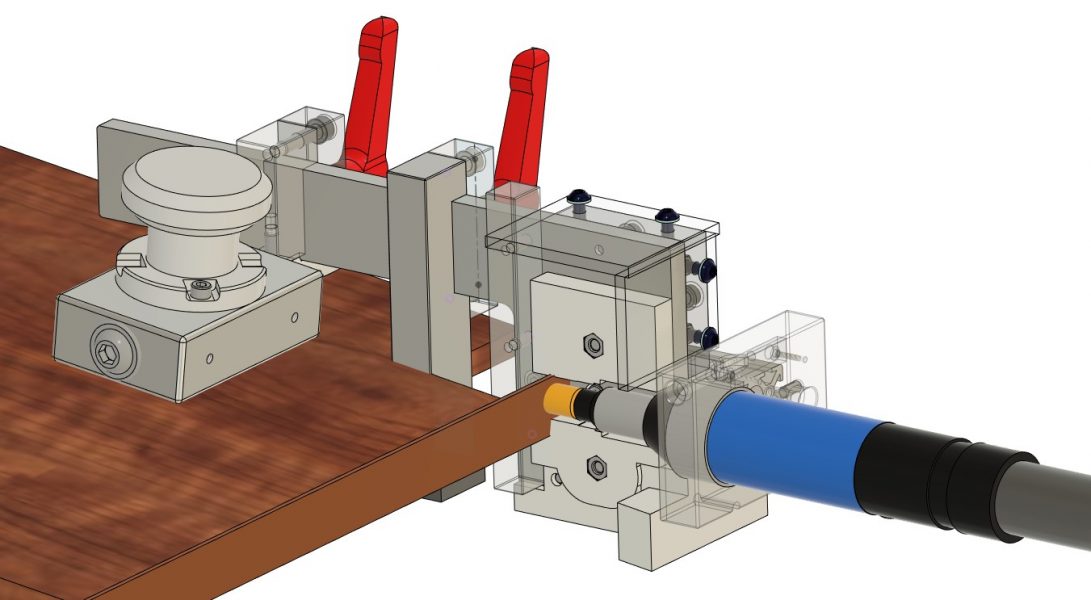
The working principle is based on the Standard flush milling cutter and is described there.
The application on the complex workpiece
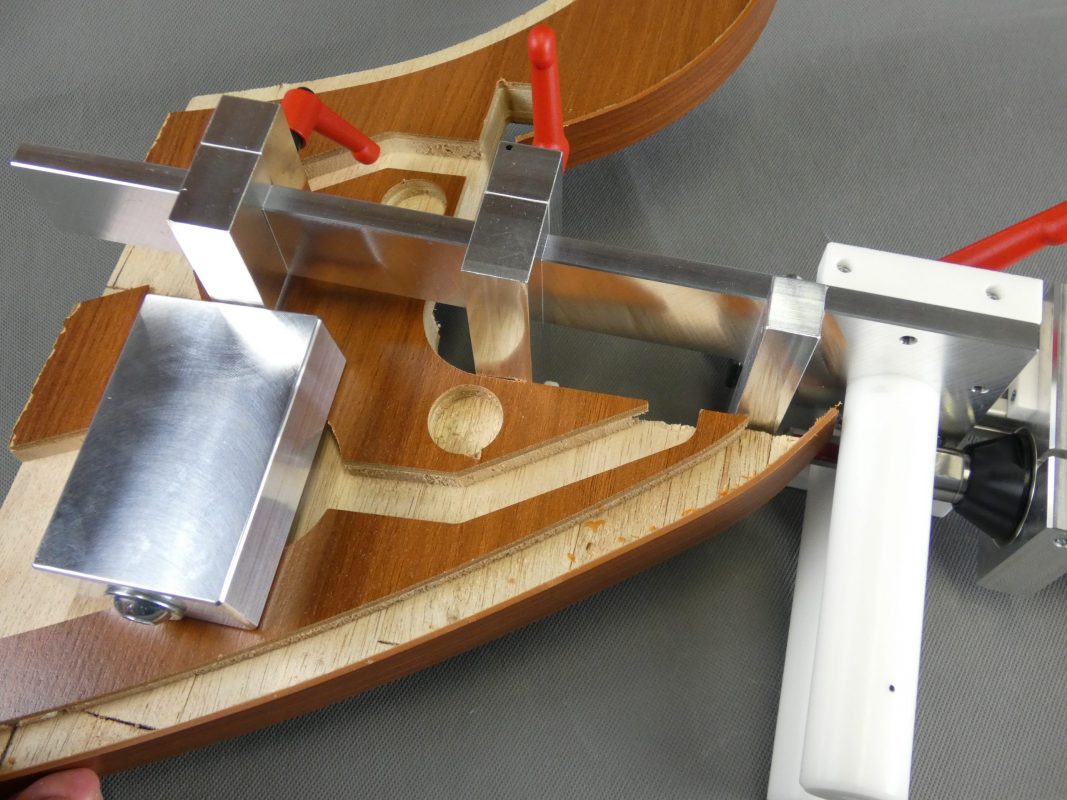
The story behind the flush milling cutter H
Narrative created with AI (artificial intelligence) on the basis of real specifications, revised with human intelligence. We are demonstrating what is possible with new methods and that we as a company use them for our customers:
A manufacturer of caravans and motorhomes had an agile and committed employee in the work preparation department. The employee, whose name we have changed and whom we call Henry here, had long been looking for a way to simplify internal processes.
During his internet search, Henry came across the company Dr Christoph Heßler Maschinensysteme (CHM HESSLER), which had developed the innovative flush milling cutter. Impressed by CHM HESSLER's expertise and commitment, Henry made contact and began an intensive dialogue. Henry quickly recognised the potential of a new milling cutter for the production of caravans and motorhomes. He could vividly imagine how the use of this innovative tool would improve the quality of the work and reduce production time at the same time. His passion for his work drove him to find a solution to integrate the new milling cutter into the company.
It initially turned out that the Existing flush milling cutters could not machine all the workpieces that the caravan manufacturer needed. Once the requirements had been clarified, CHM HESSLER developed a special variant H of the flush milling cutter that met the company's requirements. Henry provided important feedback on the development of this variant and worked closely with CHM HESSLER's design department and production staff. In this way, he ensured that the new flush milling cutter was perfectly tailored to the needs of the caravan manufacturer.
Throughout the project, Henry wore a mask due to the coronavirus pandemic, making his face unknown to CHM HESSLER. Despite this physical barrier, he continued to work closely with CHM HESSLER to discuss and implement concepts, changes, test deployments and protective elements.
When the flush milling cutter H was finally successfully introduced, the caravan manufacturer was delighted with the quality and precision it provided. The employees were grateful for Henry's commitment and embraced the new milling cutter with enthusiasm. Production processes became more efficient and work was made easier, leading to increased satisfaction and motivation among employees.
After the successful launch of the flush milling cutter H, Henry finally had the opportunity to visit CHM HESSLER at their trade fair stand and meet them in person. Being greeted without a mask symbolised the completion of a joint project and the success of the collaboration between the caravan manufacturer and CHM HESSLER. Henry deserves recognition for his valuable role in the introduction of the H flush milling cutter.
The story of the flush milling cutter H and the collaboration between Henry für den Wohnwagenbauer and CHM HESSLER emphasises the importance of partnerships, innovation and adaptability. It shows how joint commitment and collaboration can lead to new solutions, even in challenging times such as the coronavirus pandemic.
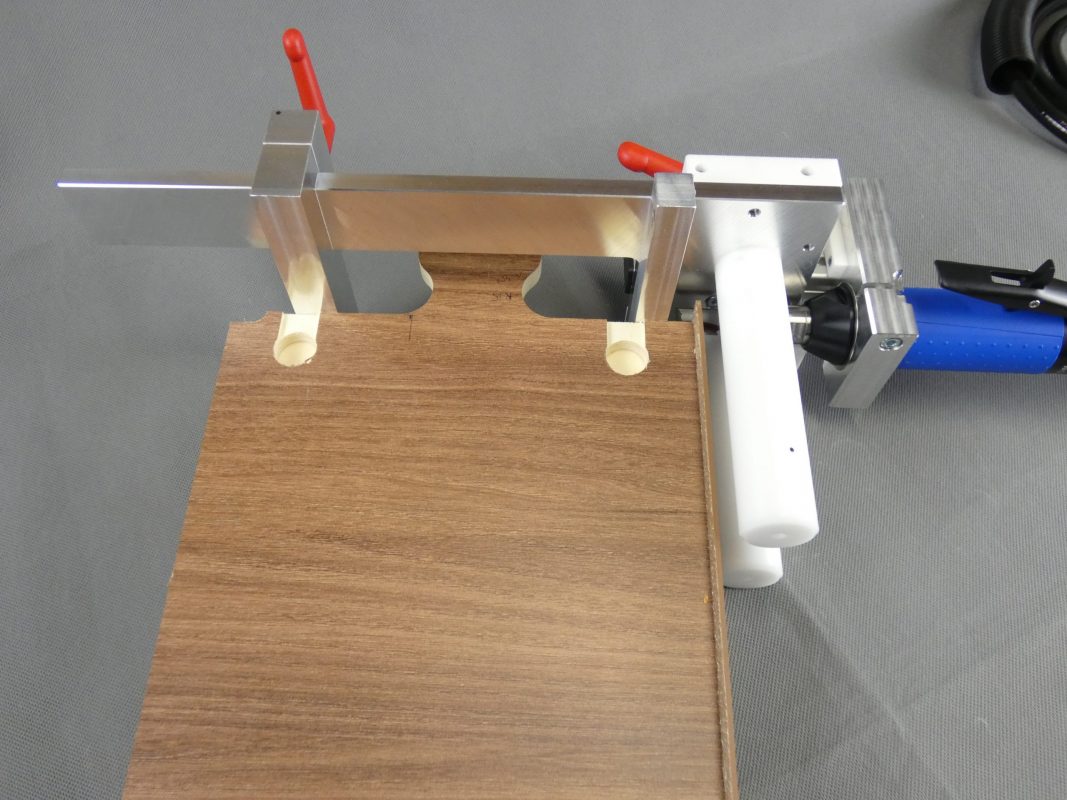
What the H all-angle flush milling cutter can do:
- Flush milling of the edge strip overhang on parts with notches and bulges
- Quick adjustment of the centre stop to adapt to the workpiece geometry
- Quick adjustment of the front stop with fixing block
- Quick change between different corner angles without adjustment
- Clean milling result
Further information
All-angle flush milling cutter
|
|
|
|
|
|
|